Nexus Round Slings
High-performance and lightweight synthetic round slings designed, tested and manufactured by Franklin Offshore
NXRS High-Performance Round Slings
NEXUS, our newest line of High-Performance Synthetic (HPS) slings, is a premium alternative to traditional steel wire ropes. NEXUS is engineered to deliver unparalleled strength, adaptability and reliability to meet any integrated rigging and mooring woes.
Meticulously developed in Singapore by our expert engineering team, this advanced series combines rigorous research, industry- leading technology, and marine-grade durability to optimize lifting operations in the harshest offshore and maritime environments.
Designed for precision and safety while providing customisable configurations, our NEXUS slings are primarily composed of High Modulus Polyethylene (HMP). This allows a seamless integration with the diverse project requirements and demands.
Modular and Configurable
Verified Hazard Reduction
Seamless Load Transfer
Engineered for Confined Environments
Resilient Design, Simplified Maintenance
Rotationally Stable Lay Design
Engineered to Stay Afloat
Modular and Configurable
Verified Hazard Reduction
Seamless Load Transfer
Engineered for Confined Environments
Resilient Design, Simplified Maintenance
Rotationally Stable Lay Design
Engineered to Stay Afloat
Product Manufacturing & Materials
Manufacturing
The Yarn
Roblon “Tornado” twisting machines are incredibly efficient and precise machines that produce yarn of the finest quality. These machines are solely utilised to create the NX-98 yarn used in NXRS high performance slings. Through extensive research and development, the twisting process has been refined to maximise the yarn’s properties for use in lifting sling applications.
Core Manufacture
The high performance parallel laid cores cores form the backbone of the slings performance. Much care and attention needs to be taken to ensure consistant loaded at each yarn
Roblon Twisting Machinery
High-Performance Cores
Product Materials
The high performance parallel laid cores form the backbone of the slings performance. Much care and attention needs to be taken to ensure consistant loaded at each yarn
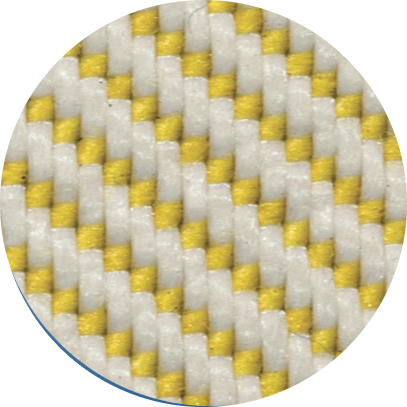
The Yarn
The body covers are made from a durable Polyester that is double bonded to offer maximum protection against abrasion and cuts.
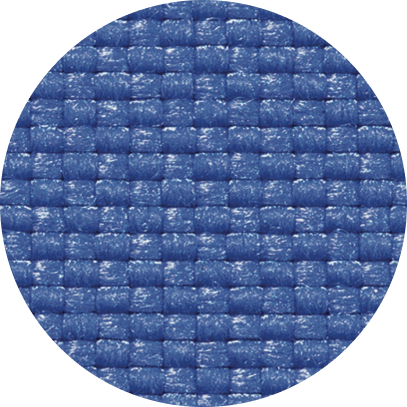
HMPE / PA
Bearing points are protected by a uniquely woven HMPE reinforced with Polyamide to offer shielding against the combined rigor of bending, abrasion and friction with more flexibility.
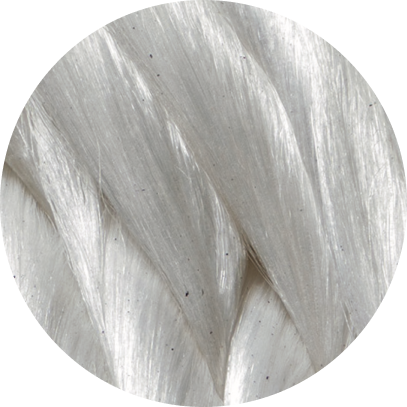
UHMWPE
Parallel laid yarns formed into a hank are the strength foundation of the NEXUS round sling.
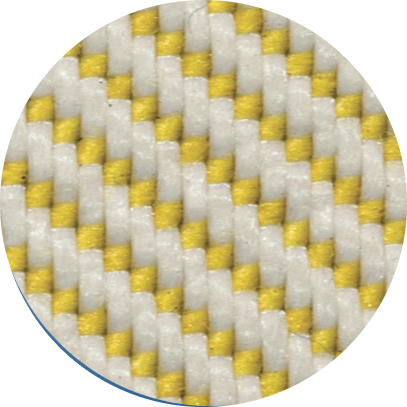
The Yarn
The body covers are made from a durable Polyester that is double bonded to offer maximum protection against abrasion and cuts.
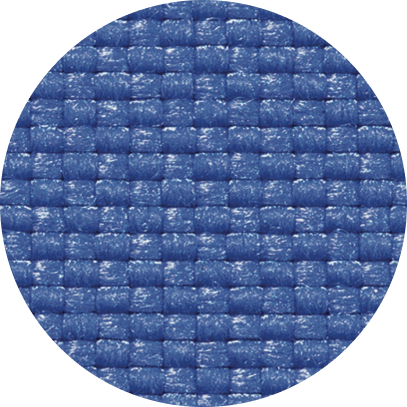
HMPE / PA
Bearing points are protected by a uniquely woven HMPE reinforced with Polyamide to offer shielding against the combined rigor of bending, abrasion and friction with more flexibility.
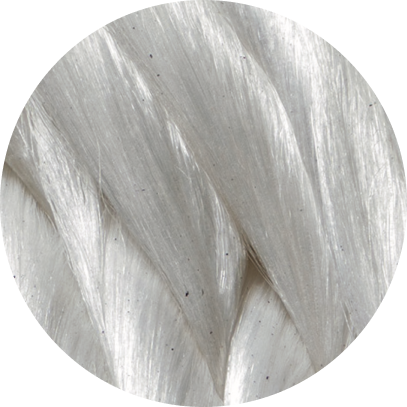
UHMWPE
Parallel laid yarns formed into a hank are the strength foundation of the NEXUS round sling.
Quality Control
At Franklin Offshore & Marine, we uphold the highest standards of reliability and safety through rigorous testing and quality control protocols. Every synthetic sling is precision-engineered with components that undergo meticulous inspection and testing prior to assembly.
Instron Tensile Tester
An essential step in the production of the yarn that will be used to make the synthetic slings is to evaluate the quality of the twisted yarn made by the Roblon machines, Franklin uses an Instron Tensile Tester for this purpose.
Instron is well-known for its accurate and dependable equipment. Throughout the production process, every twisted yarn is subjected to batch testing to guarantee that the process consistently operates within the established boundaries.
01
Component Testing: The Foundation of Excellence
At the core of our production process is component testing, where we evaluate the structural integrity of every yarn strand prior to sling manufacturing. Utilizing state-of-the-art Roblon twisting machinery, we produce high-performance yarns that are then subjected to exhaustive quality assessments.
02
Advanced Technology for Uncompromised Accuracy
Our commitment to precision is reinforced by the Instron Tensile Tester, a globally recognized system chosen for its unparalleled accuracy and reliability. This technology enables us to validate tensile strength, elongation, and load-bearing integrity, ensuring every product meets or exceeds industry benchmarks.
03
Batch Testing: Consistency Guaranteed
Throughout production, every twisted yarn undergoes rigorous batch testing to confirm compliance with predefined tolerances. This systematic approach guarantees uniform quality across all slings, aligning with stringent international standards (DNVGL, ABS) and operational demands of the shipping and marine sectors.
04
Quality Control (QC)
An essential step in the production of the yarn that will be used to make the synthetic slings is to evaluate the quality of the twisted yarn made by the Roblon machines, Franklin uses an Instron Tensile Tester for this purpose.
Instron is well-known for its accurate and dependable equipment. Throughout the production process, every twisted yarn is subjected to batch testing to guarantee that the process consistently operates within the established boundaries.
A Commitment to Excellence & Compliance
Facilities within Franklin Offshore adhere closely to the world’s leading classification societies. With ISO 9001, ISO 14001 and ISO 45001, our processes, from production to administrative, undergo rigorous audits to ensure the highest industry standards for safety, quality and sustainability.
Certifications
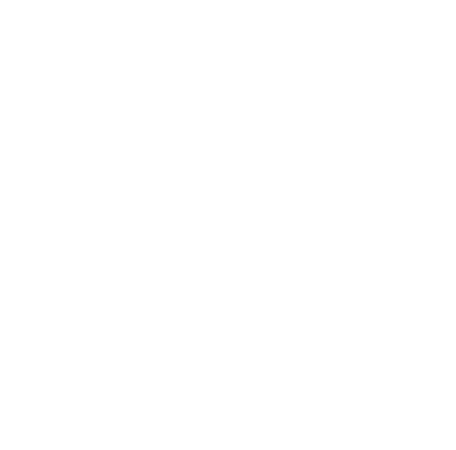
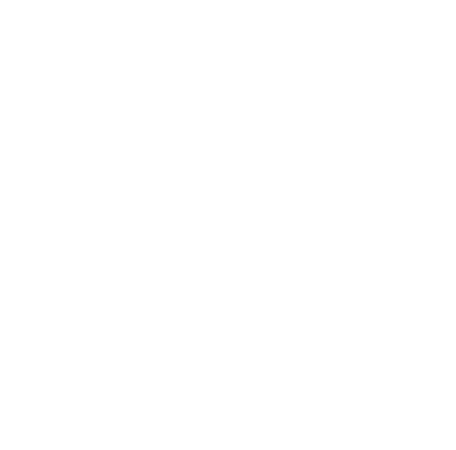
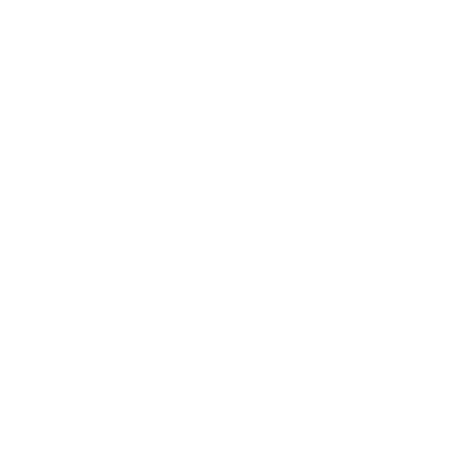
Quality Assured, Every Step
Every synthetic sling is validated through in-house proof load testing at Franklin-certified facilities and accompanied by a comprehensive test certificate. For added assurance, clients may opt for independent third-party verification from globally recognized authorities such as DNV, ABS, Lloyd’s Register (LR), Bureau Veritas (BV), or Germanischer Lloyd (GL).
Engineering Excellence Through Rigorous Validation
Each synthetic sling rope design undergoes precision-engineered validation across critical performance parameters in our R&D facilities. To meet the extreme demands of marine and offshore environments, our advanced testing protocols evaluate fatigue resistance, stiffness dynamics, twist resistance under load, performance at minimal D/d ratios, and proof/break load integrity.
Additional Features
Your Partner for Engineered Lifting Applications
At the core of our production process is component testing, where we evaluate the structural integrity of every yarn strand prior to sling manufacturing. Utilizing state-of-the-art Roblon twisting machinery, we produce high-performance yarns that are then subjected to exhaustive quality assessments.
Every synthetic sling is equipped with a marine-grade RFID tag, factoring in harsh offshore environments while providing a permanent, tamper-proof unique identification number. This ruggedized tag ensures full lifecycle traceability, critical for compliance audits, maintenance scheduling, and incident investigations within the sector.
To guarantee continuous traceability, the slings contain concealed, encrypted micro-tag embedded within its body. Even if the primary RFID tag is compromised by abrasion, chemical exposure, or impact, Franklin’s dual-tag system ensures seamless identification, aligning with stringent offshore safety protocols.
Every NXRS sling has an in-house test certificate and has undergone proof load testing at a Franklin facility. Each sling can have a third-party witness of testing, such as DNV, ABS, LR, GL, or BV, if necessary.
Need More Info?
Download the Nexus Overview
PDF includes technical specifications, applications, and performance data.